The welding of Hardox 500
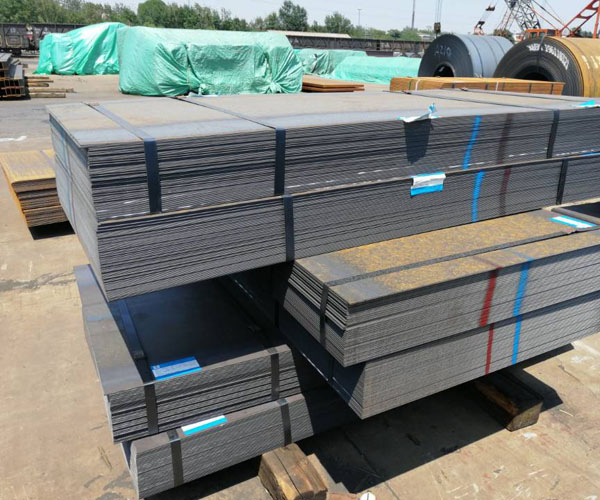
HARDOX 500 and Hardox 750 are two of the leading wear-resistant steel grades from SSAB, the world’s leading Swedish steel producer. Both materials are highly-versatile, having a wide range of applications, and are incredibly difficult to work with – especially in welding.
This is because both HARDOX 500 and Hardox 750 use a high degree of alloying elements, such as manganese and chromium, in their fabrication. This provides an excellent level of resistance to abrasion, ensuring that they last longer in service in comparison to mild steel. As such, they are the ideal choice for parts and components that require enhanced longevity in applications such as construction and mining.
Although this great durability is undoubtedly advantageous, it also creates problems through its high hardness when welding. The higher levels of alloying elements also make the surface less forgiving, which can create greater levels of splatter, cracks in the weld zone and higher levels of deformation.
When welding HARDOX 500 and Hardox 750, it is essential to use a preheating period prior to welding commencing. This helps to reduce the risk of the temperature shock, created from accelerated cooling rates, which can lead to such deformations and cracks. Preheating also helps to liquefy the alloying elements around the weld area and avoids the increased hardness, which can lead to similar problems.
When starting to weld HARDOX 500 and Hardox 750, it is important to use an acid-based pre-treatment to ensure a smooth and secure connection between the two materials. Mechanical scalping is also an option for removing any coating prior to welding commencing. This helps to provide the exact limit needed for the weld and eradicates any internal oxidation.
It is also recommended to use welding rods that have a higher degree of alloying elements. The junction should always be finished with a post-welding treatment, after the arc has cooled, by using a cleaning solution. This helps to remove any impurities, preventing any corrosion-prone areas from forming.
In conclusion, HARDOX 500 and Hardox 750 are extremely hard and difficult to weld. To successfully weld the materials, without creating any weak areas, a number of techniques must be employed, including pre-heating, acid-based pre-treatment and one-sinus washing. Ultimately, when welding HARDOX 500 and Hardox 750, it is vital to put safety first in order to avoid any further potential problems.