The NM450 vs NM400 material
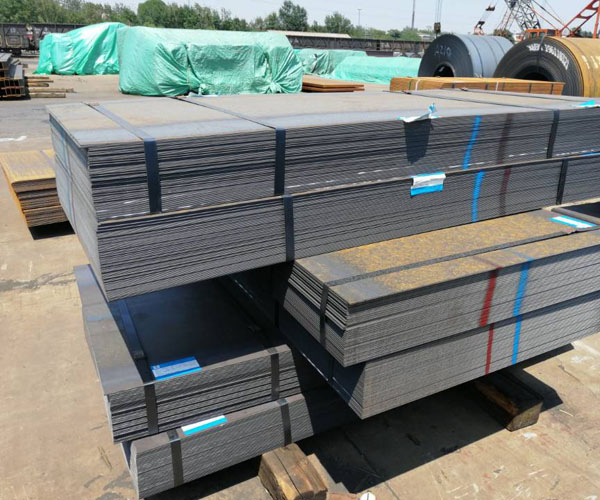
NM400 and NM450 are two types of abrasion-resistant steel plates used in industrial applications such as construction and mining equipment. Both materials have been developed to offer good mechanical properties and protection against wear and impact. While they may appear similar, they each offer distinct advantages in certain applications.
NM400 steel is an abrasion-resistant steel plate with a hardness of 400 HBW, meaning it can be pushed an average of 360-430 N/mm2 (250-310 HBW) before showing signs of deterioration. It features a nominal composition of 0.27% carbon and 1.6% manganese. Compared to other steels, its strength and hardness come at significantly cost-effective prices, making it a very popular option for many industrial uses. Due to its unique low amount of alloying elements, it can be exposed to temperatures up to 550 degrees Celsius before turning brittle. Additionally, its hardness and wear-resistance make it suitable for cutting and welding without the risk of cracking.
NM450 steel, on the other hand, has a hardness of 450 HBW and comes with a nominal composition of 0.30% carbon and 1.9% manganese. Its higher-grade properties allow it to withstand up to twice the wear than NM400, making it the ideal material for high-impact and high-abrasion applications. Its superior wear resistance also makes it a favorite for construction and mining equipment, along with antiskid plates, bulldozers and other earth-moving machines. It can also handle temperatures up to 600 degrees Celsius, making it suitable for use in a broad range of industrial applications.
When used in industrial applications, NM400 provides good mechanical properties and protection from wear and impact. Its ability to resist temperatures up to 550-degrees Celsius makes it suitable for cutting and welding applications, and its low cost makes it attractive for industrial uses. However, its lower hardness rating means that it may need to be used in combination with other steel grades to achieve the desired results. Additionally, its lower manganese content means it may require more frequent maintenance and that replacement parts may not last as long as those made from NM450.
In comparison, NM450 is suitable for high-impact and high-abrasion applications due to its harder properties and higher wear resistance. Its ability to sustain temperatures up to 600-degrees Celsius makes it suitable for a wider range of industrial applications than NM400. Additionally, its higher manganese content makes it more durable, which translates to longer lasting parts, fewer repairs, and a reduced cost of ownership. The increased hardness also makes NM450 a suitable choice for antiskid plates, bulldozers and other earth-moving machines, which require the strongest protection against wear and impact.
When determining the best choice for industrial applications between NM400 and NM450, it is important to consider the required level of protection and the overall cost of ownership. While both steel plates are highly durable and offer good mechanical properties, NM450 provides superior wear resistance and is more suitable for high-impact and high-abrasion applications. Its higher hardness also contributes to increased durability, which translates into fewer repairs and reduced costs. On the other hand, NM400 is more cost-effective and is suitable for cutting and welding applications. By understanding the differences between the two materials and their respective features, companies can make more informed decisions when choosing the right material for the job.