The Hardox 500 vs nm400 material
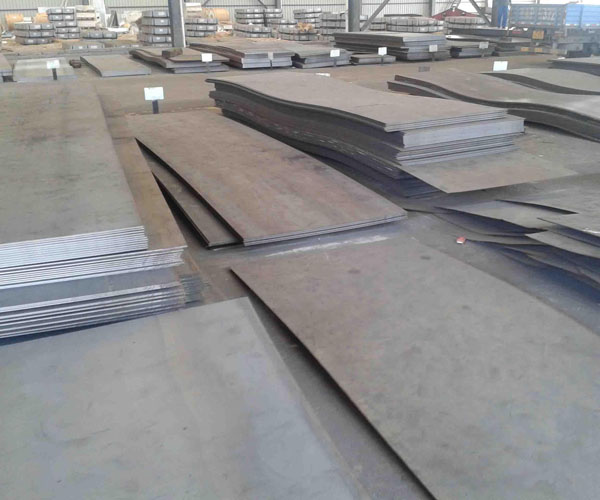
HARDOX 500 and NM400 are two of the most popular types of wear-resistant steel used by industrial parts manufacturers today. Both steels have their own pros and cons, and it’s important to understand their differences so you can select the right material for your needs.
HARDOX 500 is an abrasion-resistant steel that offers excellent strength and hardiness. This steel is often used for parts such as excavator buckets, bulldozer blades, and tipper beds, which are all subjected to heavy wear and tear over time. It has good cold formability, which makes it suitable for large and complex parts, such as those used in mining and heavy-duty construction applications. It is also relatively lightweight, making it an ideal choice for large-scale projects. Hardox’s high wear resistance and exceptional fatigue strength also make it a great choice for parts that are continually subjected to stress, such as crane and bulldozer blade components.
NM400 is an alloy of iron, chromium and nickel. This steel is also abrasion-resistant and has outstanding toughness, which makes it a great choice for industrial parts that require both strength and flexibility. However, its cold formability features are not as good as HARDOX 500, so it may not be suitable for large or complex parts. NM400 has great weldability and is often used to create complex structures, such as high-rise buildings and suspended bridges. It is also a popular choice for parts in machines and vehicles due to its superior wear resistance.
When selecting a wear-resistant steel for your industrial application, you need to consider the mechanical properties, formability and cost of the material. HARDOX 500 excels in terms of strength and hardiness, while NM400 is the more flexible option. Depending on the size and complexity of your part, either steel could be the right choice for you.