The NM400 steel vs NM450 material
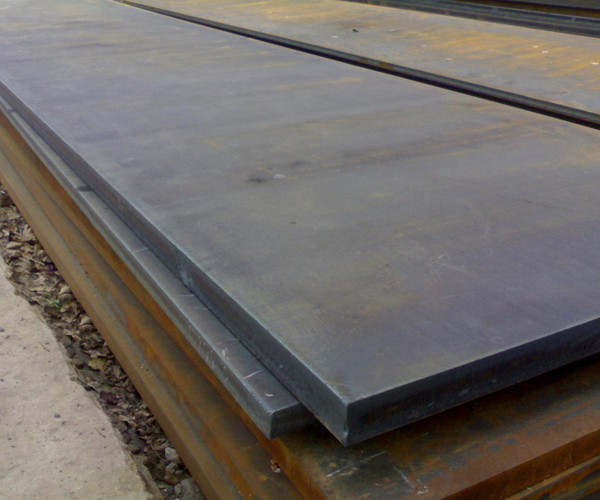
NM400 vs NM450 Steel
NM400 and NM450 steel are two commonly used materials in the manufacturing industry. Both offer excellent wear and tear resistance, making them ideal for applications requiring tough, long lasting materials. But what are the differences between the two, and which should you choose for your project?
NM400 steel is a low-alloy steel with a hardness of around 400 HBBr. It’s toughness is superior to other low alloy materials and its wear resistance is exceptionally high due to alloyed content. It is a low-alloy steel featuring high performance in wear and tear fields. It is very well suited for outdoor applications due to its superior climate resistance and excellent strength-to-weight ratio. NM400 steel is also highly corrosion-resistant, making it an ideal choice for projects with harsh environmental conditions.
NM450 steel is an elevated hardness steel often used for applications requiring an increased wear resistance and toughness. It has a relative hardness of around 450 HBBr, making it one of the strongest steel products on the market. NM450 steel is also highly abrasion-resistant and boasts superior impact resistance. In addition to this, its corrosion resistance is also outstanding, making it an ideal choice for use in corrosive environments.
When deciding between NM400 and NM450 steel, the application should always be the foremost deciding factor. While NM400 steel offers a greater range of corrosion resistance and superior weathering abilities, NM450 steel offers a greater range of wear and tear resistance.
If the application requires a material with superior wear resistance, NM450 steel is typically the preferred choice. On the other hand, if superior corrosion resistance and superior weathering is needed, then NM400 steel is the best option.
NM400 steel is typically used for medium-load-bearing applications with exposure to weather, such as bridges and cranes. This makes it ideal for transportation infrastructure. NM450 steel is more commonly used for heavy duty machinery and high-wear components, such as excavator buckets, bulldozer blades and cutting edges.
Overall, NM400 and NM450 steel both provide excellent properties and resistances for a range of applications. The choice between the two should always come down to the application requirements and what type of wear and tear or weather exposure the application will see. Whichever material you choose, whether it be NM400 or NM450 steel, you can be sure that it will provide long-lasting performance and reliability.