The welding of NM400 steel
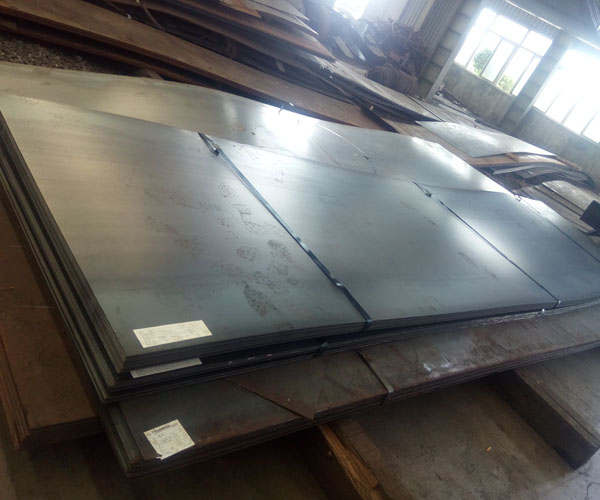
NM400 steel is a high strength steel well suited for applications that require flexibility and strength. It is a popular choice for many manufacturing applications because of its superior properties. In particular, NM400 steel is sought after for its wear resisting properties, which make it ideal for applications that require extra durability, such as construction equipment parts, mining industry tools and other equipment exposed to heavy wear and tear.
NM400 steel is a type of martensitic steel, which means it has greater strength than standard austenitic steel, the type most commonly used in fabrication and construction. NM400 steel is also a low alloy steel, meaning it contains a minimal quantity of alloying elements, such as carbon, nickel, molybdenum, or chromium, and is still easy to form and weld. This combination of properties makes NM400 steel an attractive choice for welders who require a practical and durable material for specialized applications.
NM400 steel can be welded with standard welding techniques and equipment, such as shielded metal arc welding (SMAW), gas tungsten arc welding (GTAW), and gas metal arc welding (GMAW). However, depending on the application, different welding methods may be more suitable. For example, when welding thick layers of NM400 steel, metal inert gas (MIG) welding may be a better option.
When welding NM400 steel, it is important to choose the right type of welding electrode. When welding carbon steel or low-alloy steel, such as NM400 steel, an electrode with either E43 or E48 type designations should be used. It is also important to use a low-hydrogen electrode to prevent cracking in the weld. Lastly, the welder should use a power source with the correct amperage and voltage. Too high an amperage can cause burning and warping in the weld, whereas too low an amperage may cause fractured welds or insufficient heating.
In addition to proper choice of welding materials, welders should also consider the following factors when welding NM400 steel: preheat temperature, interpass temperature, joint preparation, and cooling rate. Preheat temperature is the temperature of the metal prior to welding, and it should be determined based on the type and thickness of steel being welded. Interpass temperature refers to the temperature of the metal between welding passes and should be kept to a minimum to help reduce distortion in the weld. Joint preparation is another important factor to consider, as proper fit-up will help ensure a strong, secure weld. Lastly, the cooling rate of the weld should also be controlled in order to help reduce cracking.
By adhering to the proper welding procedures and taking the necessary precautions, welders can ensure successful fabrication of NM400 steel. As long as all factors are considered carefully and the right materials are chosen, NM400 steel can be effectively and safely welded to create powerful and durable components for a variety of applications.