NM500 weldability
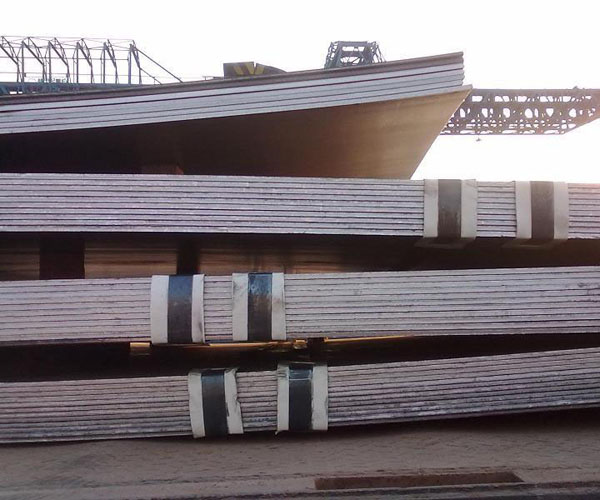
Welding NM500 is a challenging process due to its hardness and structural stability. Since the steel alloy is a combination of several elements, it is important to understand each element's properties, how they interact during the welding process and how to best prepare and weld the material.
NM500 is an abrasion-resistant steel material, usually called a 'wear steel'. It has a high level of tensile strength and a very high resistance to abrasion and shock resulting from impacts by hard objects. This makes NM500 an ideal choice for working in extreme conditions. It's used often for mining and construction operations, such as floor plates and bucket liners.
NM500 has a high carbon content of 0.27-0.44%, so it can become highly work-hardened during welding which could result in cracking if not done correctly. As such, preheating is essential before beginning to weld the material. Preheating helps to prevent cracking by raising and stabilizing the material's temperature. This helps to reduce the risk of hardness changes, stress relief and warping throughout the welding process.
The Hardfacing process is typically used to weld NM500, with a Nickel Base Alloy being the chosen consumable. This alloy is specifically designed to meet the needs of wear resistant materials, allowing for excellent deposits with exceptional impact and wear resistance. This is because it contains materials with a high hardness, such as Tungsten Carbide, Nickel, Chromium and Cobalt.
During welding, the speed and travel rate should be kept low and flux should be used to protect the surrounding material from oxidation, as well as to prevent porosity. The slag formation should also be monitored to ensure adequate protection from oxidation. Additionally, post-weld heat treatment (PWHT) should be done to reduce the hardness of the weld and avoid warping. Most NM500 welds require temperatures of 500-600 degrees Celsius to properly stress-relieve the area.
Overall, NM500 is a very challenging material to weld due to its high hardness and resistance to abrasion. As such, it demands extra attention and care when welding in order to ensure a good weld and prevent cracking and warping. Preheating and post-weld heat treatment are essential for this material and can help ensure the weld is strong and corrosion-resistant. It is best to work with an experienced welder who can properly execute a weld on the material in order to achieve the desired results.