NM500 weight calculator plate weldability
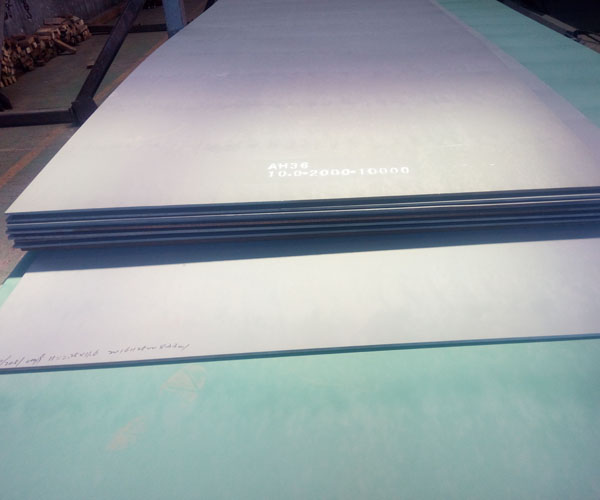
Welding joints are the way two pieces of metal are joined together to form a structure. Welding is a permanent and reliable form of joining metal components and has been used since ancient times. Today, welding is a common practice in many industries, from automotive to aerospace. Welding has many advantages, including a strong bond, improved corrosion resistance, and better fatigue resistance compared to other joining methods.
The most common welding joint is the butt joint, which is formed when two flat metal plates meet side-by-side at the same angle. A fillet joint is formed when the two plates overlap and interlock, forming a V-shaped connection. Both of these types of joints are used in many welding applications, such as automotive, small home repairs, and larger fabrication jobs.
The choice of welding joint also depends on what needs to be welded. For example, a butt joint is ideal for welding two thin metal plates, while a fillet joint is better for heavier pieces. Furthermore, the type of weld chosen also depends on the type of metals being welded together. Different metals require different welding techniques.
In addition to choosing the right joint, the right materials are important for a strong and permanent weld. For example, most welding jobs require the use of filler metals, which provide additional strength and fill out any gaps between the two different pieces of metal. Filler metals are made up of many different alloying elements, each of which has its own unique properties and characteristics.
The welding process also includes preparation, which includes cleaning and ensuring the welding areas and surfaces are free of contaminants. An effective weld is only possible when the areas being worked on are free of soil, dust, and other particles. The areas should also be free of any moisture or lacquer.
As with any type of craft, practice is key to becoming a proficient welder. Welders should regularly check their welds for signs of cracking or porosity, both of which indicate a flawed weld. Additionally, the temperature of the weld should match the temperature of the surrounding material. Too much heat can result in burned material, while too little heat can result in a weak weld.
Finally, there are a variety of welding processes, from arc welding to laser welding, each of which has different characteristics. Welders should take the time to research the various types of welding processes, materials, and joints, so they can choose the best option for their project.
In short, welding is an essential skill for many industries, and welders should understand the importance of selecting the right joint, materials, and process for welding tasks. Researching all these topics will help ensure welders are prepared and have the right techniques, materials, and knowledge for a successful weld.